A brief review about stability and safe handling of waste acids originated by the production of nitric esters.
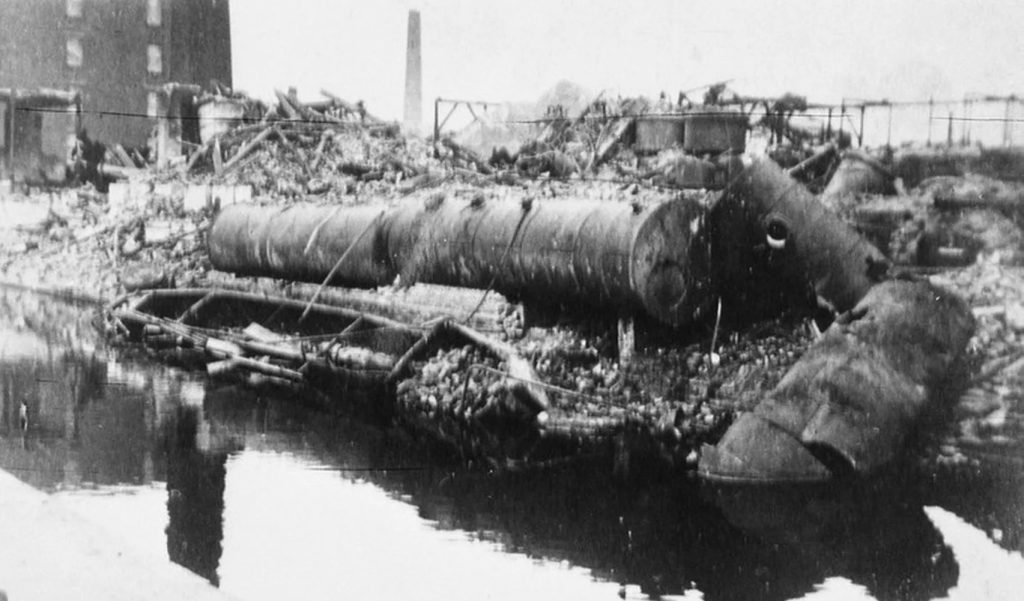
The problem of handling and recovery of spent acid has existed since the advent of nitration on industrial scale. The concern with safety is related to the storage of the spent acid, because the latter always contains a certain amount of nitro-compounds, which are subject to auto-catalytic decomposition. There are three types of nitration: nitration to carbon, nitration to oxygen, and nitration to nitrogen, which originate respectively nitro-carbons, nitric esters, and nitramines. Nitro-carbons are characterized by relatively high stability, if compared to nitric esters and nitramines, so their handling is relatively safe. On the contrary, nitric esters and nitramines are both unstable if left in contact with nitrating acids, and each of them requires customized cycles of stabilization.
In this post we deal particularly with nitric esters. Since the origin of nitration of glycerine, the problem of safety related to handling and storing the spent acid containing 2-3 wt% of nitric esters became a very serious issue. This is due to the fact that nitric esters may separate as a second phase and float on the surface of the acidic phase. So far, they become very sensitive and can easily decompose explosively.
Generally speaking, the spent acids from nitration of glycerine, glycols and pentaerythritol have a lot in common, although they differ in some particular points. The common problem of nitration of alcohols and glycols was studied by Camera et al. [4,5]. In their study, they identified some of the products of the action of nitrating acid on ethyl nitrate, which was selected as a model for the behaviour of nitric esters in the acid solution. They came to the conclusion that the initial process consisted in the hydrolysis of the ester. Indeed, the hydrolytic equilibrium is disturbed by oxidation of the alcohol by both residual and liberated nitric acid. In these intermediate range of concentration, the nitric acid becomes an oxidizer and is reduced to nitrous acid, which, from its part, can serve as a catalyst of a number of additional reactions. Among the other products formed, in addition to acetaldehyde and formaldehyde, there are acetic and oxalic acids, carbon dioxide and nitrogen oxides, like NO2-N2O4, N2O3, NO and N2O, although the latter is generally present only in traces. So, it is evident that the safety of nitration plants is strongly dependent on both chemical composition and temperature of the waste acids, because these are the main factors that determine the content of dissolved esters in the aqueous phase, as well as the content of dissolved acids in the organic phase, if any.
Several scientific studies conducted on this topic agree on in their conclusions stating that the presence of nitric esters as a second phase is the major cause of explosions connected to handling of nitration waste acids. On the contrary, when nitric esters are present only dissolved in the aqueous phase, they decompose exothermically, sometimes also quite violently, but the macroscopic result is only the so called ” fuming off “, during which a copious quantity of red noxious fumes are released by the waste acid.
A very helpful diagram in use in almost every production facility is the Waste acid Stability Diagram [6]. Originally the latter was developed only in graphic form, but it is nowadays available also as a software [7]. Mathematical models have also been used to analyse the relative enthalpy of spent acids [8]. By means of these tools and ordinary chemical analyses it is possible to determine both the stability of the waste acid and its life-time, that is the reasonable amount of time during which the waste acid can be stored without any appreciable autocatalytic decomposition. In any case, the waste acid can never be considered stable and safe, until the nitric esters are fully decomposed.
Nowadays, a process unit called decomposer is conveniently used to performs the full decomposition of the nitic esters continuously. There are different types of decomposers, specifically designed to treat different types of waste acids, which can be either mixed nitric and sulfuric acid, as it is for NG, EGDN, PGDN, etc, or nitric acid alone, as it is for PETN.
Syntech International Srl can design and supply Continuous Decomposers as either stand-alone process units, or process units fully integrated in a waste acid reprocessing plant. In this case, not only the nitrogen oxides produced by the nitric ester decomposition are conveniently recovered with a full conversion into nitric acid, but also the consumption of energy is largely reduced.
References.
[1] Encyclopaedia of Explosives and Related Items, Volumes 1-10 (1960).
[2] The Chemistry and Technology of High Explosives. Parts I-III (1961).
[3] Chemistry and Technology of Explosives, Volumes 1-4 (1964).
[4] La Chimica e l’Industria 41, 1064-1066 (1959).
[5] La Chimica e l’Industria 61, 179-183 (1979).
[6] Industrial & Engineering Chemistry Research 36, 5068-5073 (1997).
[7] Journal of Loss Prevention in the Process Industries 11 (3), 161-168 (1998).
[8] Process Safety and Environmental Protection 87 (2), 87-93 (2009).
Author.
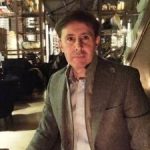
Luigi Ambrosi, M.Sc.
Process Chemist – Registered in Italy (BS)
Co-Founder and Chief Scientist at Syntech International Srl
l.ambrosi@syntechinternational.com